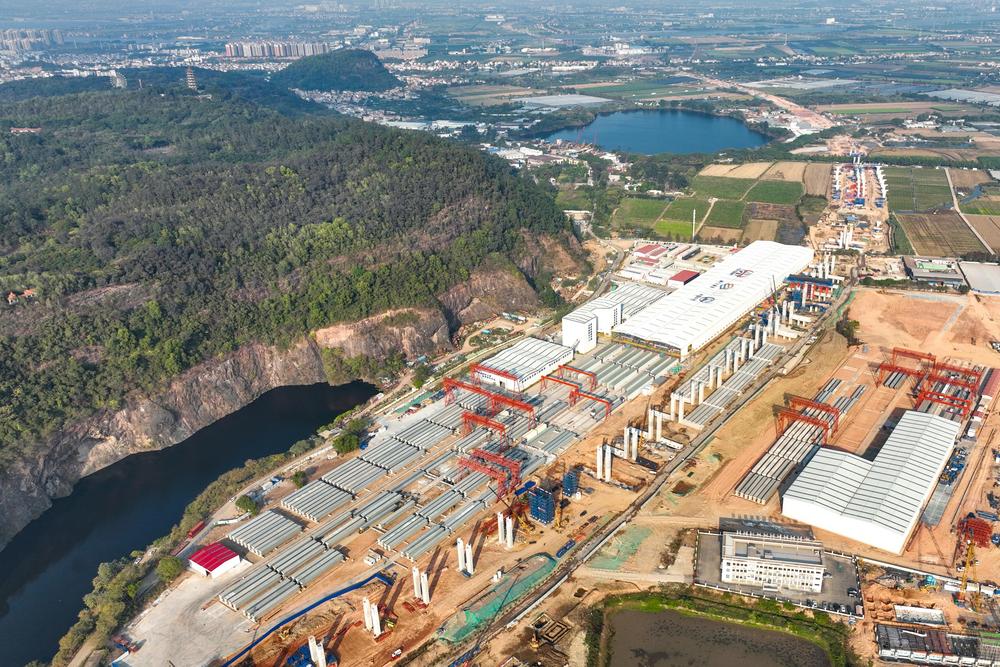
智慧梁厂全景 谢农 摄
4月26日,在中铁四局五公司广州狮子洋通道T13合同段项目部施工现场,机械臂精准抓取钢筋并稳稳放入底腹板胎架,不到两个小时,一片箱梁的钢筋骨架便已成型。在这里,每片箱梁都拥有属于自己的“身份证”,重达几十吨的箱梁可以“行走自如”,生产时间更是从7天缩短为1天。这是项目部注重科技创新赋能、推动箱梁生产由传统要素驱动向创新驱动转变的缩影。
作为粤港澳大湾区新的跨海通道,广州狮子洋通道工程是连接狮子洋东西两岸的超大型跨海多层复合公路通道,全长35公里。其中,项目部管段为全线最大预制箱梁标段,承担着T2至T4合同段共计7790片箱梁的预制生产任务。进场以来,项目部集成应用局内有关制梁场方面的科研成果,打造出集数字化管理系统、钢筋自动化生产线、智能液压模板系统和混凝土智慧管控平台于一体的“智慧梁厂”,首次实现公路预制箱梁全部采用柔性环形生产线,创新国内公路行业预制梁生产模式。
量的飞跃!“七天一片”到“一天一片”
“智慧梁厂”占地面积288亩,由生活区、办公区、混凝土配送中心、中枢管控平台、预制车间、产业工人社区等功能分区组成。预制车间内部采用柔性环形作业模式管理,设置钢筋智造车间、底模小车横移转向区、液压内模安拆区、浇筑区、蒸汽养护区、雾化养护区、张拉区、回转区等分区以及12条柔性环形生产线,铺设轨道连通各分区,以移动台座进行梁片周转,配备产业工人实现“一条龙”流水线作业,产能全开情况下,可以达到一天生产1片梁。
“我们早在3年前的南中高速4标项目就已应用智慧梁厂环形生产线模式。这次在原来环形生产线的基础上优化模板、钢筋设备、工艺工装设备,升级成柔性环形生产线,大幅提升生产效率。”项目部总工程师李云飞介绍。
该项目部在楔形块模板下方设置液压油顶,实现一键零误差调整楔形块;在梁端设置纵向液压油缸,自行伸缩至指定梁长位置;在底模小车端部设置下沉和滑移块,张拉前松开固定螺栓,避免梁端薄弱部位受力过大引起开裂;调整中边梁倒角,解决中边梁模板无法共用的问题,减少后期施工中频繁更换侧模;使得液压系统和调节块相配合,实现横隔板位置的毫米级调整,解决横隔板位置不精准等质量通病。
该项目部7790片的箱梁预制任务包括25米箱梁840片、25米至30米箱梁5941片、35米至40米箱梁1009片,依托于柔性环形生产线,可以实现在同一套模板上通过调节完成不同梁长、梁宽和角度箱梁的预制任务,解决异型梁模板设计和快速更换的难题。
从“七天一片”到“一天一片”,柔性环形生产线居功至伟,但项目部自行研制的钢筋自动化生产线也不容小觑。该生产线集成U型钢筋及定位网加工、智能转运、骨架组拼焊接、顶板生产等功能,实现钢筋加工全流程智能化作业,应用智能上料系统,可以自动完成钢筋排布、插筋和网片成型等工序,配合高精度焊接系统,实现顶板钢筋骨架和底腹板钢筋骨架的自动化生产,使钢筋自动化组装成型率达80%以上,较传统人工作业方式减少用工60%以上,产线单日产能4个网片以上,显著提升生产效率和产品质量。
质的提升!“制造”到“质造”
既要保证高效率,也要确保高质量。存梁区内,一块块表面细腻光滑的箱梁整齐摆放。“不只是光滑,箱梁梁板可以达到镜面效果,甚至能反光照出人影。”3月3日,广东省交通集团有限公司2025年度基建工作会议观摩团走进该项目部观摩,看到箱梁成品后交口称赞。
“不同环境条件下,要选用不同的配合比、脱模剂,才能制出外观质量满足建设单位要求的预制梁。”项目部试验室主任熊涛指着10余个试验模型介绍。温度和湿度都会影响混凝土的稳定性,该项目部通过不同配合比、脱模剂小尺寸模型试验、3米试验梁缩尺试验等方式论证,经过材料选型、市场选型,结合地理位置等综合考量,确定最终的配合比和脱模剂,确保箱梁内实外美。
“每片梁的优质出品,都要在浇筑、振捣、脱模、运输、养护等关键环节精准发力、精益求精。”熊涛说出该项目部箱梁预制的诀窍。他们采用“鱼雷罐+智能化布料机”的方式实现混凝土精准浇筑,与传统的混凝土运输罐车加人工料斗运输布料的方式相比,不仅浇筑效率提高40%,还降低人为因素对混凝土质量的影响,有效保障混凝土性能,减轻劳动强度,减少安全风险。
该项目部首次实现公路预制箱梁液压内模应用,液压模板拆装半个小时即可完成,与传统人工拼装式模板比,单孔制梁周期缩短30%以上,解决普通内模安拆工效低、安全风险大的难题。由“全自动液压模板+智能液压动力控制单元”组成的智能液压模板系统,相比于传统的敲、打、撬的拆模工艺,作业人员通过触摸屏进行模板安拆作业,实现内模一键开合和整体脱出,有效避免梁体损伤和模板变形,保障预制梁体外的棱角和线形分明。在底模小车上加装高频附着式振捣器传递振动波,可以对梁片振捣部位、次数、时间等数据智能调控,极大提高预制梁底板的密实度和光洁度。
“梁体的质量好坏,养护也非常关键,传统人工养护费时费力费水,还很难达到理想效果。”项目部工程部部长金锐介绍。在预制梁的养护环节,该项目部采用“智能雾化蒸养+智能喷淋养护”模式。预制梁浇筑后由移动轨道送至蒸养棚,经过静置、升温、恒温、降温等步骤确保质量。蒸养设备一键启动,无需人工监控温度,系统根据设置的温度曲线自动调节棚内温度,高效节能的同时还提升混凝土强度、弹性模量,实现快速成梁,达到张拉条件。“温度升至50摄氏度,每小时上升不超过10摄氏度,恒温保持8小时,均由系统智能控制。”金锐说。随后,箱梁通过智能喷淋养护系统实现二期养护,进一步有效解决养生不均、水资源浪费等难题。
“智”的转变!“梁场”变“梁厂”
从“片产”到“量产”,从“制造”到“质造”,“梁场”变“梁厂”离不开智能的“大脑”——中枢管控平台。它不仅是生产指挥的“中枢”,也是数智升级工程的“大脑”。该项目部前期在充分调研丰田汽车、格力集团等的先进管理模式基础上,提出全力打造标准工业化的“MES(制造执行系统)+ERP(企业资源计划)+SCADA(数据采集与监视控制)数字化梁厂”的管理理念。
走进“中枢管控平台”,一张高清大屏映入眼帘,上面实时显示着各施工环节数据。每片箱梁从钢筋塑形到浇筑成型,再到养护出厂,可以实现全过程信息化管控,相当于每片箱梁都有自己的“身份证”。在智能排产板块,平台接收下部结构施工单位的架梁计划后,可根据研发的算法自动解析形成制梁计划,结合现场的混凝土配送中心、地磅等的物联数据,实现资源的调度,还可根据每片箱梁的长度、高度、斜交角等参数以及生产线状态综合排产,使产能达到最优。在三维数字孪生模型上,平台根据物联数据反馈驱动三维模型制梁工序的运转,点击梁片可以查看梁片基本信息、工序信息、质检表格、保护层厚度、蒸养曲线、工程量清单、外观质量等数据,通过数据接口还可实现模板、振捣器、鱼雷罐、布料机的远程操控,管理人员仅靠指尖就可对施工生产情况了如指掌。
该项目部积极推进信息化成果运用,全面提升智慧建造水平,成功打造行业领先的标准化、自动化、数字化和智能化的公路箱梁柔性环形生产线,引起行业内外广泛关注。3月以来,先后迎来交通运输部科学研究院专家团、交通运输部路网监测与应急处置中心专家团,广东省交通运输厅、江苏省交通工程建设局以及中国铁建港航局、中铁山桥、广西贵岑高速公路有限公司、辽宁中交秦沈高速公路有限公司等单位组织的观摩30余次。
如今,该项目部的智慧建造成效初显,作业人员输入参数加工钢筋,浇筑成型后的箱梁进入雾化蒸养,中枢管控平台实时跟踪……“室内车间即使碰到雨天依然可以正常生产作业,大幅提升施工效能,截至目前我们已经预制866片箱梁。”项目经理黄卫兵自豪地说。
李鑫 徐莉 邓飘